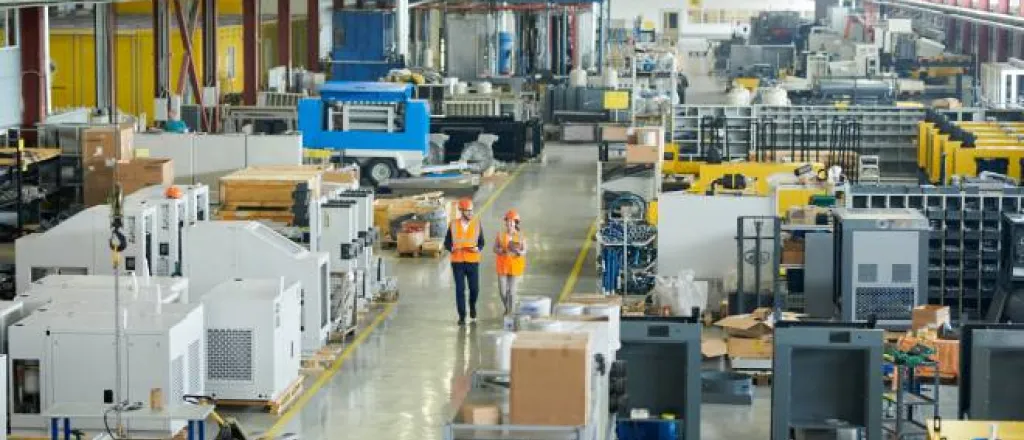
4 operational practices sabotaging factory performance
©
Factories are dynamic environments where every decision impacts efficiency and profitability. Despite a commitment to smooth routines, several operational practices sabotaging factory performance go unnoticed and chip away at your productivity. Identifying and addressing these practices can unlock untapped potential while guaranteeing sustainable operations.
Mismanaged downtime—the silent profit killer
Downtime for machinery, planned or unplanned, is one of the largest drains on factory performance. When factories fail to manage downtime effectively, they incur diminished productivity, increased labor expenses, and rushed repairs.
Beyond these financial setbacks, unoptimized downtime can delay schedules and lead to excessive wear on other equipment, which results in a domino effect of inefficiency. Proactively tracking mechanical downtime, its frequency, and root causes allows businesses to prioritize preventive measures and reduce disruptions.
Improper heavy equipment choices—one size doesn’t fit all
The wrong equipment can damage workflows and amplify operational costs. Whether it’s overloading with machinery beyond production needs or under-purchasing tools that fall short, such decisions can stifle efficiency.
For example, assessing your exact needs will help you make the right choices without wasting money or time on trial and error. Invest in learning things like the benefits of pallet jacks over forklifts and other equipment comparisons to offer your employees the perfect tools for the job. Evaluating tools based on factory size, workload, and production goals promises the right fit for optimizing performance.
Employee overload—working harder isn’t smarter
When employees feel stretched too thin, productivity plummets. Overworking staff across multiple tasks or excessive shifts increases errors, delays, and fatigue-related risks. This approach compromises output quality and workplace morale.
Implementing better workload balance strategies, such as delegating tasks or incorporating skill-focused training programs, can prevent bottlenecks. Empowered teams are safer, more efficient, and less prone to burnout, which enables sustained levels of performance.
Overlooking factory layout—the hidden efficiency drain
Many factories overlook how critical layout optimization is for flow and productivity. Poorly placed machinery, redundant walking paths for workers, and inefficient storage systems hinder smooth operations. Keeping the tools necessary for a task centralized will keep workers from wasting time looking for or traveling to get them.
Purposeful layout designs tailored to material flow and workforce efficiency can eliminate these invisible barriers. Minimizing motion waste and aligning equipment placement with ergonomic principles streamlines factory operations and maximizes space.
Take control of operational efficiency
By addressing these operational practices sabotaging your factory’s performance, you can recover from inefficiencies that silently erode profitability. Smart planning and investment in your employees and their experience can improve your efficiency. Focus on these areas today to guarantee a sustainable and thriving operation tomorrow.