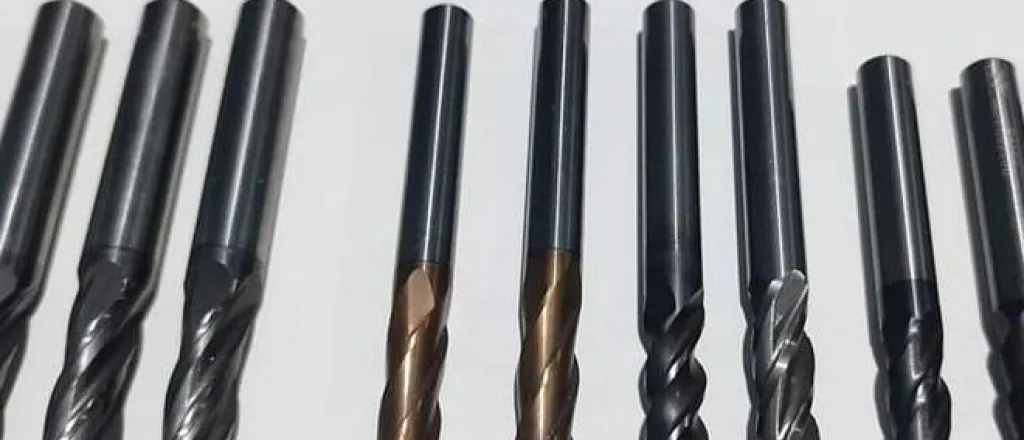
How to find a high-quality coating for your end mill
©
In the search for durability and efficiency in tools, a high-quality coating on an end mill is the hero that provides long-lasting durability. This thin barrier can significantly extend the tool’s life and performance, especially under the rigors of heavy machining. With the right coating, roughing and finishing operations become smoother and more accurate. But where do you find such a product for your tools? Read on to learn how to find a high-quality coating for your end mill.
Understanding end mill coatings
End mill coatings are technical marvels that reduce wear and friction, protect against high heat, and ward off material build-up that could otherwise compromise your cuts. Coatings such as aluminum titanium nitride (AlTiN) and titanium nitride (TiN) are common, but they each offer different benefits. Your choice should depend on the specific application and material you’ll work with.
Key attributes to look for
So, what should you look for? What attributes to a high-quality coating?
Selecting the best coating isn’t simply a matter of preference. Considering the amount of environmental exposure and abrasion your end mill experiences, you’ll want a coating that can withstand significant wear. Some attributes to have include hardness to protect against abrasion, something that has edge integrity when exposed to heat, and that reduces friction on the end mills material. A veneer with these properties keeps your end mills working longer and harder.
Advances in coating technology
When you’re first working with end mills, inquiring about modern coating technology improves your understanding of why coatings are crucial. Many coatings integrate nano-composite materials to alter surface properties at the microscopic level. These advancements enable end mills to perform consistent, high-quality cuts even in punishing conditions.
Application-specific selection
Consider the substrate of your end mill, the materials you’ll cut, and the types of machining you have in mind. This approach ensures that the coating effectively complements its operation. For instance, while TiN coatings are general-purpose, AlTiN coatings are better for high-temperature applications.
Types of end mills
End mills come in various types, each designed for specific materials and machining processes. For instance, a flat-end mill is ideal for general-purpose milling, such as slot and keyway cuts, offering a clean square cut with a flat tip. Ball Nose End Mills creates smooth and contoured cuts using a round profile that produces curved surfaces.
Another type is a corner radius end mill that uses a combined flat and ball nose end that creates rounded corners to reduce chipping and extend tool life. Finishing End Mills, designed for fine finishing tasks, features a higher number of flutes for a smoother surface finish. Our last mention is a roughing end mill, and one of the things to know about roughing end mills is that their unique profile minimizes vibrations. The specific applications and advantages of each end mill type vary, which affects which end mill coating to pick.
The key to finding a high-quality coating for your end mill lies in its correlation with the intended application, superior tech specifications, and end mill type. A premium coating equates to enhanced tool longevity, performance, and precision. Whether you’re in agriculture, crafting, or any sector involving milling, making an informed decision on coatings ensures your end mill won’t just meet but exceed expectations.