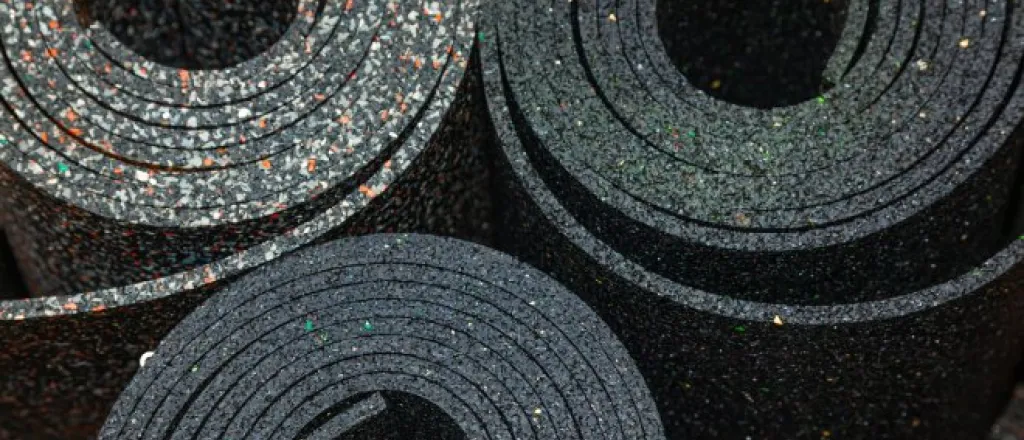
When to replace: Removable insulation blankets
©
Removable insulation blankets are essential components in various industrial settings, offering crucial thermal insulation for machinery and pipes. Their design allows for easy installation and removal, facilitating maintenance access and improving energy efficiency by reducing heat loss. These blankets are made from durable materials that can withstand high temperatures, making them suitable for use in power plants, refineries, and chemical processing facilities. Understanding when to replace removable insulation blankets is vital, as exposure to harsh environments can degrade their effectiveness over time.
Signs of wear and tear
Regular inspections are key to identifying signs of wear and tear in removable insulation blankets. Indicators that a blanket may need replacement include visible cuts, tears, or abrasions on the blanket's surface, which can compromise its insulating capability. Additionally, any signs of mold or mildew suggest exposure to moisture, which not only reduces insulation efficiency but can also lead to further damage. Discoloration or hardened areas may indicate exposure to extreme temperatures or chemical exposure, which can degrade the material's integrity.
Maintenance and tips for improving longevity
Thankfully, proper blanket maintenance and storage can significantly extend the longevity of your investment. Regular cleaning is essential to prevent dirt and debris from accumulating, which can affect the blanket's insulating properties. It is advisable to use mild cleaning agents and avoid harsh chemicals that could degrade the material. When not in use, store the blankets in a dry, cool area to prevent exposure to moisture and extreme temperatures. It is also important to ensure that blankets are fully dry before storage to prevent mold and mildew growth. Regularly inspect the storage area for pests or environmental conditions that could lead to deterioration.
Never repair, always replace!
Any significant damage, such as cuts, tears, or abrasions, necessitates replacement rather than repair. These damages can severely compromise the blanket's ability to provide effective insulation, leading to increased heat loss and reduced energy efficiency. Attempting to patch or repair these issues is not recommended, as it might only temporarily address the problem without restoring the blanket's full insulating capacity. A compromised insulation blanket poses risks not only to the system’s performance but also to safety standards within industrial environments. Consequently, it is best to replace blankets at the first sign of significant damage for optimal operation and safety compliance.
Invest in a quality replacement
Investing in high-quality removable insulation blankets is crucial for ensuring both operational efficiency and safety in industrial environments. Quality blankets are designed with premium materials that provide superior heat resistance, durability, and longevity, ultimately reducing the frequency of replacements and associated costs. High-caliber insulation solutions also ensure consistent thermal performance, minimizing energy loss and optimizing process efficiency. Additionally, using top-grade products can enhance safety by reducing the risk of thermal-related incidents or equipment failures. An investment in quality not only secures immediate efficiencies but also contributes to long-term savings and stability.
Knowing when to replace your removable insulation blankets is crucial for maintaining optimal performance and safety in industrial settings. Regular inspections, proper maintenance, and investing in quality products are key to extending your blankets’ longevity and ensuring consistent thermal insulation. With proactive care, removable insulation blankets can provide reliable protection for your machinery and pipes, improving overall energy efficiency and reducing operational costs.