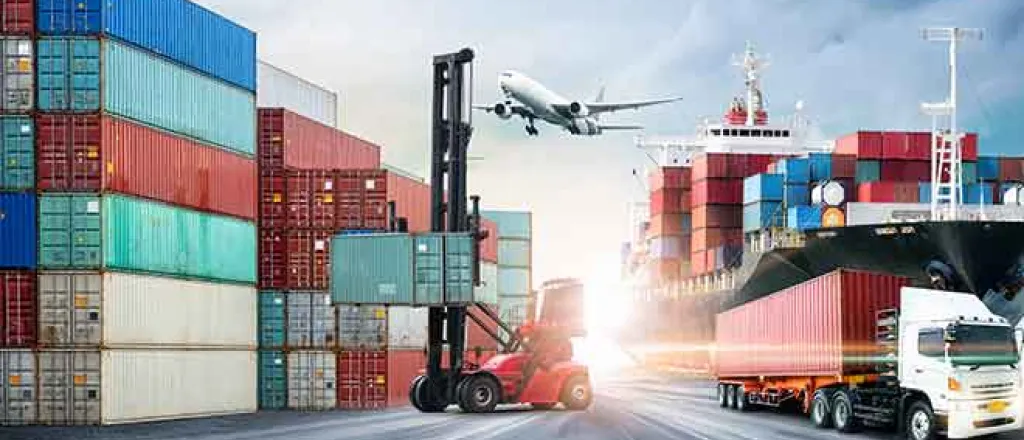
Why you should expect more Suez-like supply chain disruptions and shortages at your local grocery store
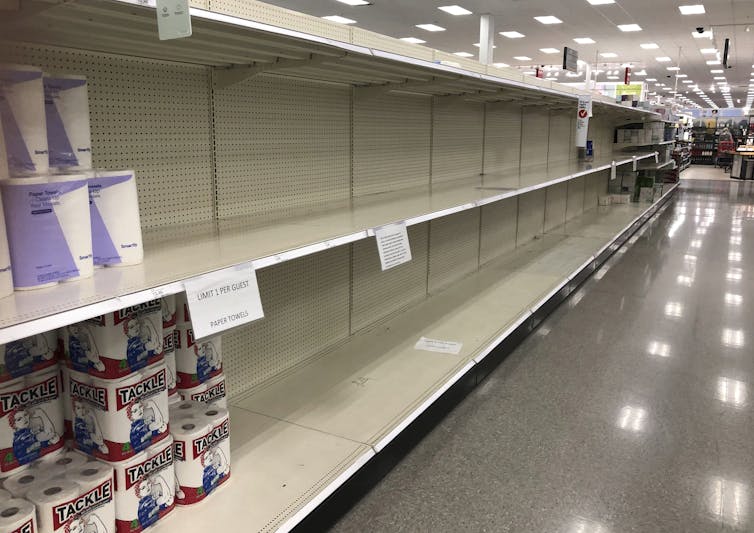
Nada R. Sanders, Northeastern University
When the Ever Given container ship choked off traffic in the Suez Canal for almost a week in late March 2021, it made big headlines around the world.
The price of oil rose, and companies fretted as hundreds of ships carrying everything from coffee and cattle to toys and furniture were delayed. Experts estimated that every hour traffic remained stuck cost the global economy over US$400 million in lost trade.
Yet many people I spoke with, including students and professional colleagues, didn’t seem to have a clue about what was happening, why it mattered or how it affects them.
As a supply chain expert, I was truly surprised. If nothing else, the COVID-19 pandemic should have made it abundantly clear how easily a disruption in the supply chain or a sudden increase in demand for a product can lead to empty grocery store shelves and other problems that might directly affect you.
Without a change of course, I expect this problem to only get worse.
Supply chain strains
The pandemic revealed that even simple supply chains, such as that of toilet paper and hand sanitizer, can easily break in the face of disruptions. The same was true with food, personal protective equipment, pharmaceuticals and ordinary household items, which all suffered from severe shortages that lasted for months into the pandemic.
Pandemic-strained supply chains are now creating a global shortage of semiconductors, a component used in a wide variety of consumer goods, from Samsung smartphones and Apple laptops to Ford Explorers and Sony PlayStations. Virtually every piece of electronics needs a chip, and the supply chain is much more complex than for toilet paper.
The Suez Canal blockage that began on March 23, 2021, and lasted six days exacerbated these already stressed supply chains. Even though traffic is now running smoothly through the canal, the jam is still causing massive ripple effects and delivery delays – even toilet paper could once again be in short supply.
It may take up to 60 days for the supply chain system to reset itself to where it is functioning close to normal.
That means consumers will continue to feel the impact of these problems for months to come as well.
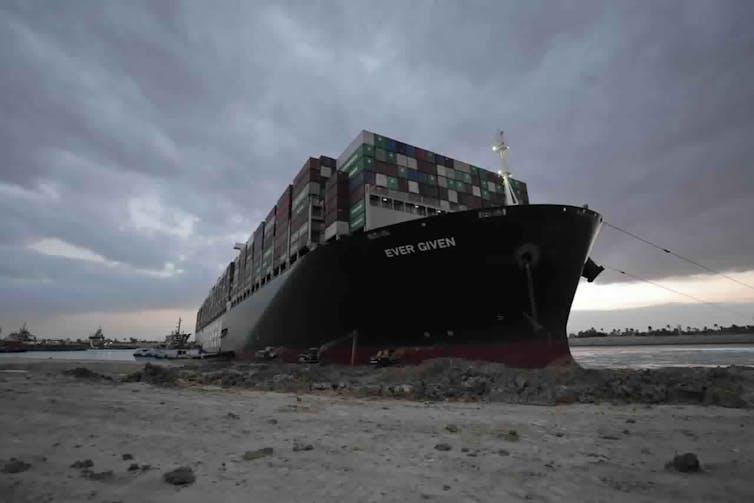
Lean and mean
The fundamental problem behind each of these disruptions is simply the inability of modern supply chains to adjust when something goes wrong, even briefly.
A big problem early in the pandemic, for example, was simply a lack of flexibility. While consumers were having trouble tracking down toilet paper because of panic buying and hoarding, there were plenty of rolls sitting in warehouses but intended for offices and restaurants. Companies had trouble diverting the toilet paper to the retailers, which kept only a very lean inventory of the product.
Supply chains for this and most every other product have been increasingly designed to be as lean as possible in terms of cost and efficiency, rather than resiliency. As customers demand ever cheaper products delivered faster, supply chains have given up every bit of slack. As a result, a disruption of any magnitude creates significant consequences through product shortages and rising prices.
It’s easy to think of a supply chain like it’s a linear conveyor belt, as disparate parts turn into a product that is then shipped around the world to your door. But it is more like a massive intertwined highway system.
Consider the path and massive disruption caused by shortages of a simple chip, known as a display driver. Its only purpose is to convey instructions for illuminating a digital screen like the one on your phone, laptop monitor or navigation system in your car. There is a huge shortage of the chips – caused by supply problems and soaring demand. And this in turn has triggered a shortage of liquid crystal display panels, as well as a jump in prices, forcing automakers, airplane manufacturers and refrigerator makers to all scale back production. All because of a shortage of a $1 chip, in part triggered by minor disasters like the recent winter storm in Texas and a fire in Japan.
And a problem like the Suez Canal traffic jam is even worse because it is represents an intersection – and bottleneck – for so many supply chains, including oil, parts and finished products. As cargo is shipped, there is a complicated choreography of vessels, ports, distribution centers and other modes of transport.
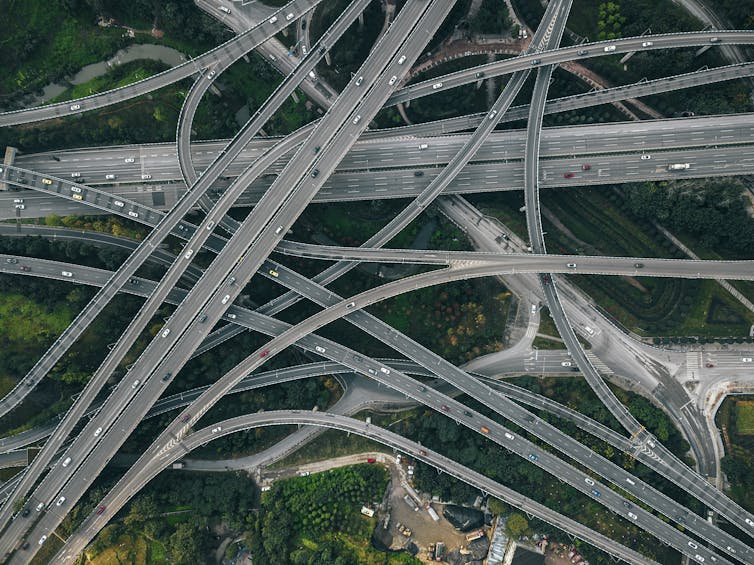
A little more slack
The obvious solution is to add resiliency or slack into supply chains – to expect the unexpected. This would require moving away from aggressive “lean systems” that have virtually no excess inventory.
It doesn’t have to be terribly costly. As my own research shows, companies need only selectively add extra inventory, suppliers and capacity for certain critical items or at key chokepoints, such as for products identified as being in short supply, where there are few suppliers or where lead times are extra long.
For example, coffee roasters generally do not have inventory to handle a two- or three-week delay. Delays in shipping raw beans from Brazil and the Ivory Coast to Europe due to the Suez blockage mean consumers will likely soon experience the impact of a lack of coffee availability in stores and cafés.
This is not a recommendation to stock huge amounts of inventory. Rather, it is to say that there are advantages to being highly strategic – almost surgical – to ensure that the greatest resiliency can be achieved with only a small amount of additional slack.
Otherwise, the trends that led supply chains to become so lean and efficient will likely continue, leading to more and bigger disruptions for the global economy and more shortages and higher prices for consumers like you.
[Insight, in your inbox each day. You can get it with The Conversation’s email newsletter.]
Nada R. Sanders, Distinguished Professor of Supply Chain Management, Northeastern University
This article is republished from The Conversation under a Creative Commons license. Read the original article.