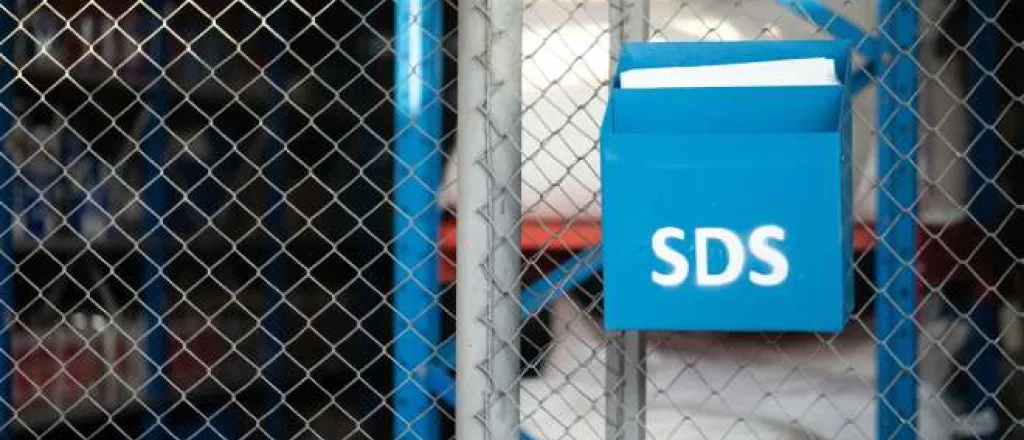
4 Uses for chemical safety data sheets
©
Chemical safety data sheets (SDSs) provide vital information about chemical properties, hazards, and safe handling practices. Workers who use or store chemicals can obtain SDSs from manufacturers, distributors, or online databases. Explore four uses of chemical safety data sheets that ensure safety and compliance in healthcare facilities, laboratories, manufacturing plants, and other locations.
Upholding workplace safety
SDSs promote workplace safety by offering detailed guidelines on the safe handling and storage of chemicals. Each SDS contains information on proper storage conditions, required personal protective equipment (PPE), and first-aid measures. This data is critical for preventing accidents and injuries and ensuring that facility managers can implement safe practices.
Segregating stored chemicals based on compatibility is one of the key practices in safe chemical co-storage. By providing compatibility information, SDSs help prevent hazardous reactions between incompatible substances.
Maintaining regulatory compliance
Safety data sheets offer a comprehensive overview of the chemical's hazards, handling procedures, and environmental impact. By providing clear guidelines and safety protocols, SDSs make it easier for facility managers to understand and meet regulatory requirements. They help ensure that all employees know the hazards associated with the chemicals they handle, promoting safe practices that align with legal standards.
Workers must know this information in order to adhere to government regulations. This helps protect facilities from potential fines and legal repercussions. Regulatory compliance also protects workers and the environment.
Facilitating emergency response
Organizations and businesses also use chemical safety data sheets as invaluable resources for emergency response. These documents provide specific instructions on how to manage spills, providing guidance for containment, cleanup procedures, and necessary PPE. Quick access to this information enables facility managers to respond effectively to emergencies, preventing further harm.
Additionally, SDSs contain first-aid measures and emergency contact information, facilitating swift action during incidents. By incorporating SDS guidelines into emergency response plans, safety managers can prepare their teams to handle chemical emergencies with confidence and efficiency.
Enhancing employee training
Educating employees about chemical hazards and safety procedures is crucial for maintaining a safe work environment. SDSs serve as foundational resources for employee training, offering detailed information on the risks associated with each chemical and the precautions necessary to mitigate them.
SDSs also support ongoing training initiatives by providing up-to-date information on chemical safety. Regularly reviewing and discussing these documents helps reinforce safe practices.
Chemical safety data sheets are essential for workplace safety, regulatory compliance, effective emergency response, and comprehensive employee training. By leveraging these resources, safety managers can protect their teams and facilities from the inherent risks of handling hazardous materials.